The biggest challenge faced by industries today is to continuously deliver better quality products at a faster rate keeping the development costs at a minimum.
Although using CAE tools helps bring down the development costs, it is important to use these tools very early in the development stage. Using CAE tools later in a development cycle can cause wastage of time, efforts and resources in redesigning, reanalyzing and fixing the design issues. Instead, using these tools earlier in the design stage to drive decisions can considerably reduce the development time and cost. Also, this helps the designers understand the performance of their designs and helps them make better design decisions.
So, for an organization to deliver under an ever increasing competitive pressure of cost, quality and speed, it is imperative that a Designer puts on his Analyst hat.
What are the challenges faced by designers in analyzing designs?
Traditionally, the CAE tools have been very specialized and targeted to be used by expert analysts and specialists. This poses a steep learning curve for the designers. Achieving a reliable method of data transfer between the environments, managing multiple environments and collaborating with expert analysts is a whole different set of gymnastics. These challenges not only slow down the design-analysis iterations considerably, but they also de-motivate the designers to be analysts. This creates a need for a set of reliable, easy to use analysis tools that can overcome the challenges faced by organizations in analyzing designs early in the development cycle.
CATIA V5 “Analysis for designers” portfolio:
Dassault Systemes provides “Analysis for Designers” portfolio which includes a set of easy-to-use analysis solutions within the CATIA V5 environment. Being a natural progression of CATIA V5, they help designers perform quick design-analysis iterations very early in the product development stage so that more design options can be evaluated within the time-cost constraints. Analysis results drive the design decisions and help designers improve product performance.
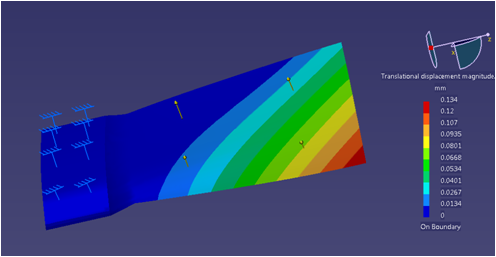
A common design – analysis environment eliminates the need of data transfer and possible data integrity issues associated with it. Designers can perform analysis directly on the master reference model in CATIA and the generative specification-driven approach makes it very easy to re- analyze design changes with automatic updates. It also eliminates the need for managing multiple software environments.
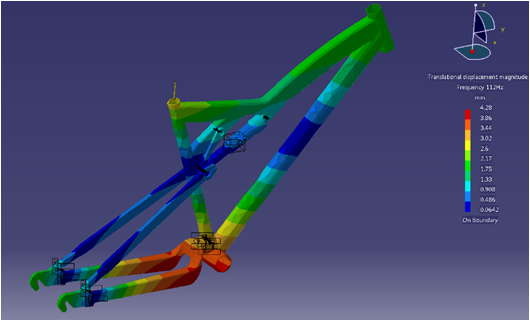
CATIA Analysis workbenches use robust built-in finite element solver and mesh generators which deliver accurate results very quickly, striking an efficient balance between accuracy and speed. Adaptive meshing capability is used to deliver accurate results by automatically remeshing and reanalyzing the parts without user intervention
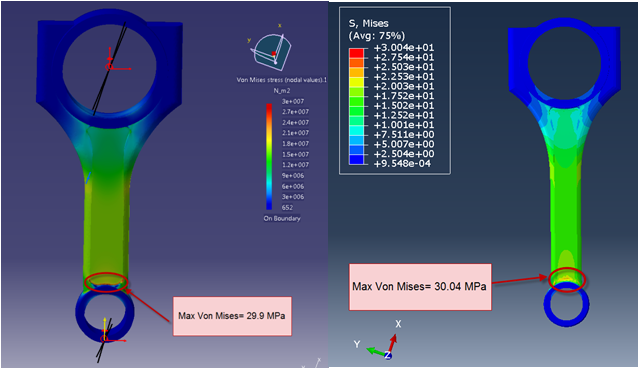
Demonstration of CATIA Analysis Capabilities
Article compiled by Manish Barlingay
Application Engineer
Inceptra