With increasing product complexity, and frequently changing customer needs, configuration management can play a critical role in your company’s success. Highly customizable products increase complexity not only in the design process but in all stages of the product lifecycle. This includes, but is not limited to, requirements definition and management, systems modeling and engineering, change management processes, and through the manufacturing process.
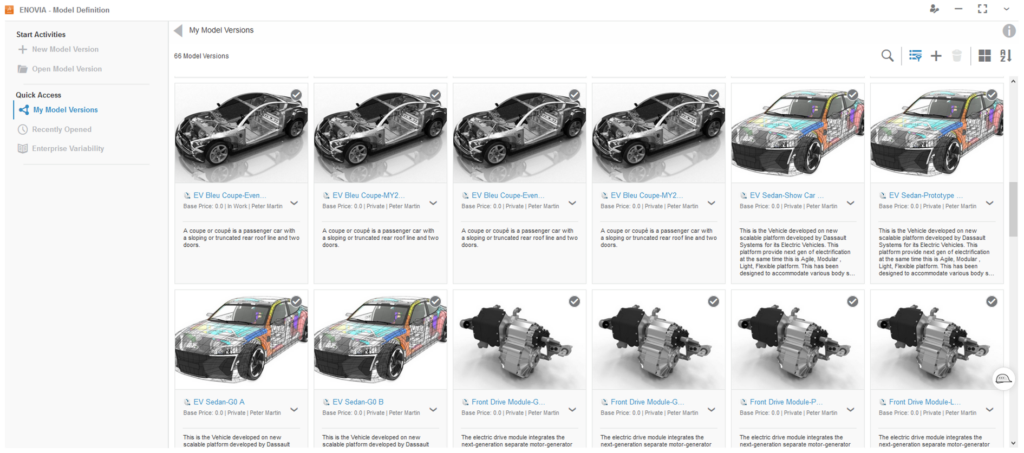
To meet these challenges, the Dassault Systèmes 3DEXPERIENCE platform provides a solution to manage the definition, planning, and development of your complete product portfolio. Powerful yet flexible tools allow you to define a product portfolio that can be rapidly expanded to address new markets and constantly changing consumer preferences while also minimizing costs and maximizing profits. Using the 3DEXPERIENCE platform, a single master variant-option dictionary, and all associated configurations rules and logic, can be managed in one place that is accessible to all stakeholders. Product configurations can then be defined and applied during all stages of the product development process.
In this blog, I’ll highlight the configuration management capabilities of the 3DEXPERIENCE platform that can enable your teams to deliver configurable products faster while minimizing design changes and development costs. It should be noted that the 3DEXPERIENCE solution can be applied to any industry including Automotive, Aerospace and Defense, High Tech, and Industrial Equipment.
Configuration Management Options on the 3DEXPERIENCE Platform
Different types of configuration management may be required based on the kinds of products you’re developing and the industries you serve. The 3DEXPERIENCE platform supports configurations based on timelines, development/design phases, manufacturing plans, and production units, working in conjunction with your master variant-option dictionary.
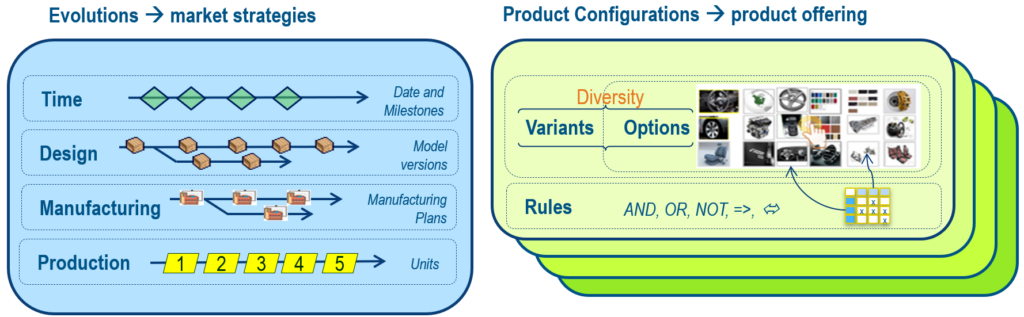
For example, as a vehicle matures from concept to prototype to pre-production and eventually production many changes will be needed. Changes may be required based on testing results, safety requirements, customer demands, expansion into new markets, and more. As these changes occur, additional variants and options will be required and applied to the vehicle. This will continue into production as each new model-year is introduced and updated.
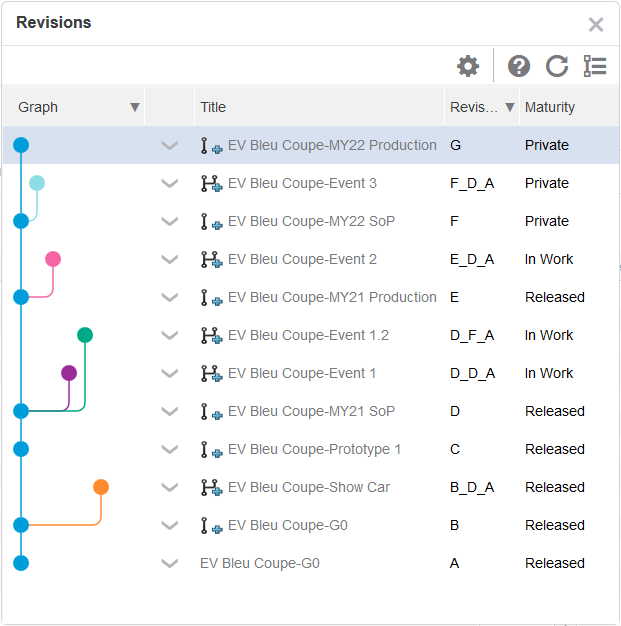
Some examples of vehicle changes might be: 1) new safety options which are required by government regulations, 2) adding a high-performance model to the lineup, or 3) expanding into a new market which requires right-hand-drive. In the case of a high-performance model, many additional options will need to be added such as an updated interior, turbo-charged engine, the addition of a spoiler, and several new paint color options.
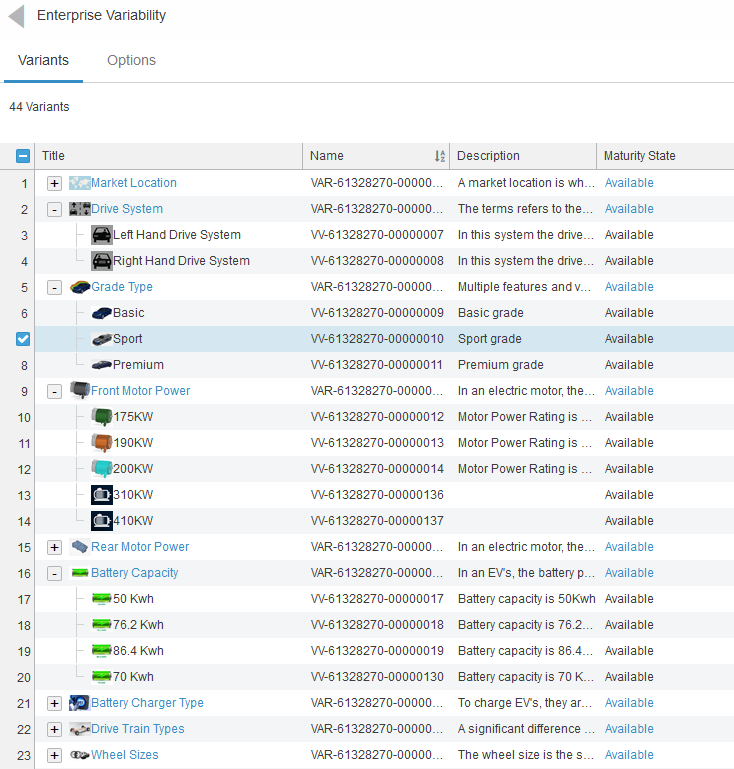
These new options can be added to your master variant-option dictionary quickly and easily, and all previously defined data will continue to be available.
Creating Configurations
As you can see, 3DEXPERIENCE configuration management allows you to create a 150% bill of materials (BOM) which contains all available variants and options for a particular product. Once the data has been created, users can quickly filter by specific configurations and will only see the configured 100% BOM for that product. All options that do not apply to that configuration will not be shown
To ensure the correct variants and options are selected, the 3DEXPERIENCE platform supports various types of rules and checks. Some examples of rule logic include: if-then rules, compatibility checks, marketing preferences, and matrix rules. Matrix rules ensure that only the proper variants are selected, enforce mandatory selections, and enforce consistency and control across the configurations
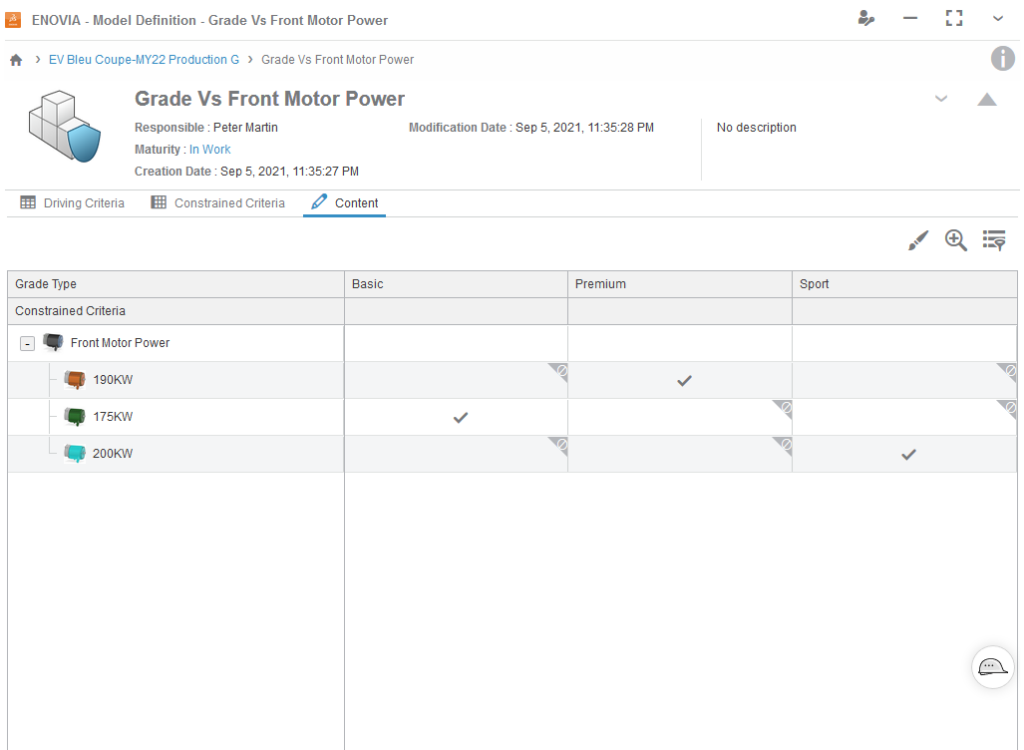
In the following example we see a specific configuration has been created for the Premium Coupe. For this configuration, many options are set and cannot be changed based on the rules such as the motor type, seat type, etc. However, some option may be configured such as wheel type, charger type, and wheel size.
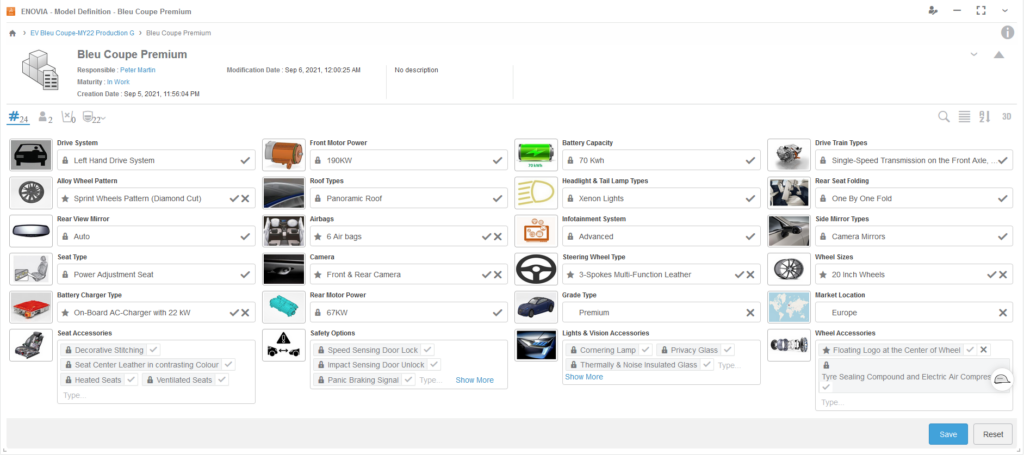
Configurations Across the Product Lifecycle
With the 3DEXPERIENCE platform, configurations not only apply to the engineering and design data but also apply to virtually all aspects of product development.
Requirements management is critical to establishing the product definition and may include technical, regulatory, and performance requirements that must be satisfied. Different configurations will need to meet different requirements and 3DEXPERIENCE allows us to filter requirements using the same logic described above.
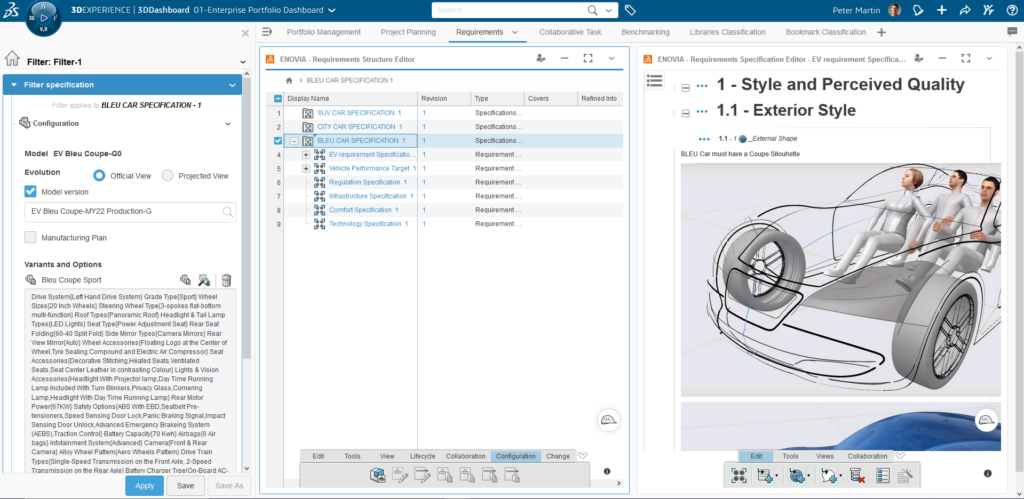
While modeling systems using CATIA Magic (CAMEO), configurations can also be applied and systems models easily filtered. This extends to additional traceability applications on the 3DEXPERIENCE platform when viewing the System of Systems.
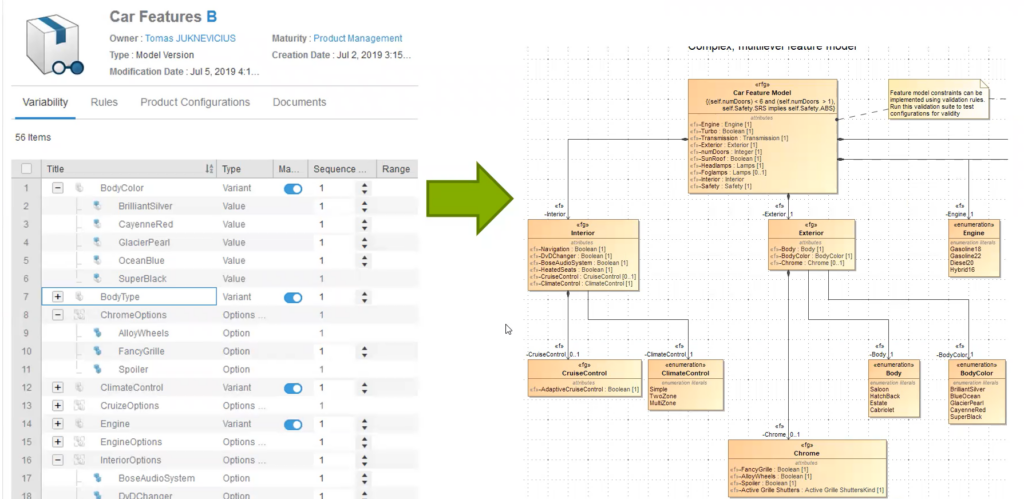
During manufacturing planning, it is also important to have the ability to filter content by specific configurations. This means as you prepare the Manufacturing Bill of Materials (MBOM) the structure can be filtered since downstream manufacturing processes are also affected such as process planning and work instruction creation. For example, various manufacturing plants may have certain capabilities and the assembly instructions for different options will vary.
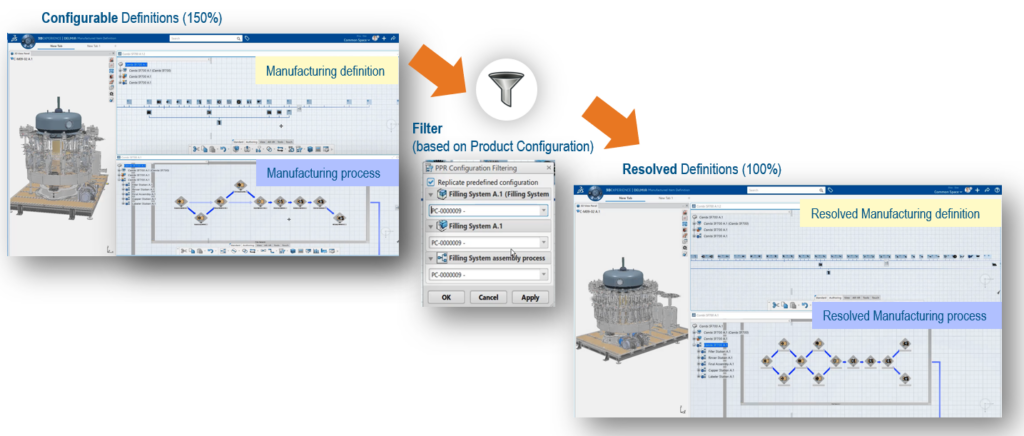
When changes occur across the development process, the powerful change management capabilities utilize configuration management to ensure the proper products are updated. Impact analysis tools allow you to visualize all affected items across your organization.
Conclusion
As your products evolve and new configurations are added, the configurations will drive the development across the product lifecycle. The new options can be added in the 3DEXPERIENCE platform making them available for the designers, systems engineers, and manufacturing engineers to use. This not only allows for reuse of all existing configurations and data but also provides flexibility during your product development processes.
By defining all product variants and effectivities in a single configured product structure accessible to all cross functional teams, manufacturers can optimize component reuse, reduce costs across product variants and evolutions, and deliver products faster.
Questions?
If you have any questions or would like to learn more about configuration management on the 3DEXPERIENCE platform, please contact us at (954) 442-5400 or submit an online inquiry.