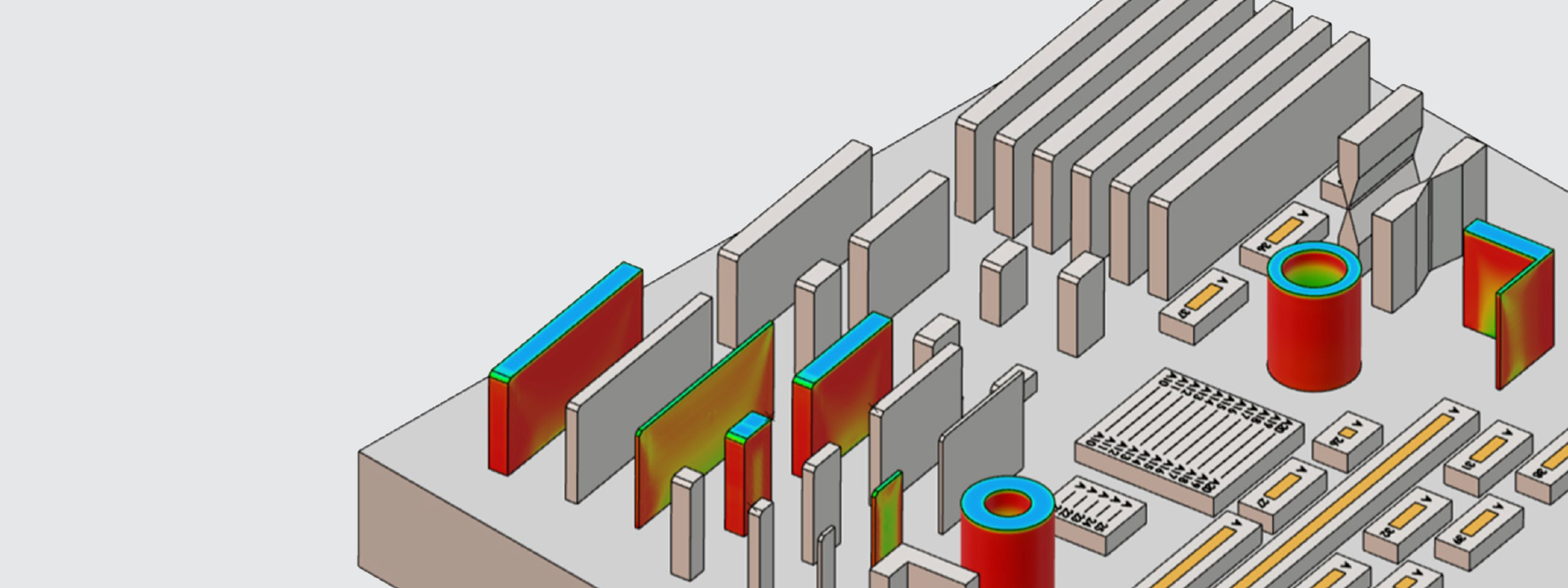
An End-to-End Solution for Additive Manufacturing
From creating custom one-off products to constructing components that traditional subtractive methods can’t achieve, additive manufacturing (AM) is adding value to numerous industrial applications. However, scaling up AM processes can be challenging due to issues with repeatability and build quality, which are major obstacles to adoption.
Dassault Systèmes provides an end-to-end solution for additive manufacturing on the 3DEXPERIENCE® platform. This whitepaper focuses on the role of simulation in this workflow. Demonstrating how structural analysis can accurately predict residual strains in 3D-printed parts. The solution presented in this paper has been experimentally verified. As well as won first prize in the Air Force Research Laboratory (AFRL) “Macro-scale Process-to-Structure Predictions” challenge.
Dassault Systèmes AM Simulation Solution
The 3DEXPERIENCE platform offers a comprehensive workflow for additive manufacturing from design to production, therefore enabling collaboration between designers, process specialists, and analysts both on-premise and in the cloud. This solution covers all stages of AM development: part design, topology optimization, build process planning, and strain and deformation calculation.
The CATIA Digitized Shape Preparation app, the DELMIA Powder Bed Fabrication app and the SIMULIA Additive Manufacturing Scenario app are all leveraged in this solution.
The SIMULIA Additive Manufacturing Scenario app performed a thermomechanical analysis. Efficiently simulating the build process. It activated elements progressively, modeled heat transfer, and used a moving heat flux to simulate the laser. Coupled thermal and mechanical simulations computed residual strain in the part.
Experimental Verification
The AFRL challenge demonstrates the physical validity of simulation results from the SIMULIA Additive Manufacturing Scenario app. Which is crucial for producing high-quality AM parts.
Figure 1 as can be seen, shows strains in the longitudinal (a and b) and printing directions (c and d) on the 1 mm leg of the L-shaped part. Dotted red lines represent simulated microstrains, black lines are experimental values, and grey lines indicate a 2σ (500 microstrain) interval. Most simulated strains fall within this interval.
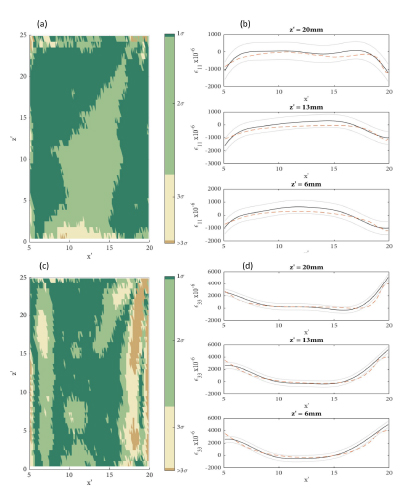
Click to Enlarge Image
Figure 2 illustrates strains in the radial and printing directions on a long section (x-z plane) of the 5 mm cylindrical part. Simulated radial strains largely match the 2σ interval of experimental strains. While printing direction strains fall within the 3σ interval for most of the part. Dotted red lines show simulated strains, black lines show experimental strains, and grey lines represent a 2σ interval. Strain variation along the printing direction at different heights from the simulation aligns qualitatively with experimental findings.
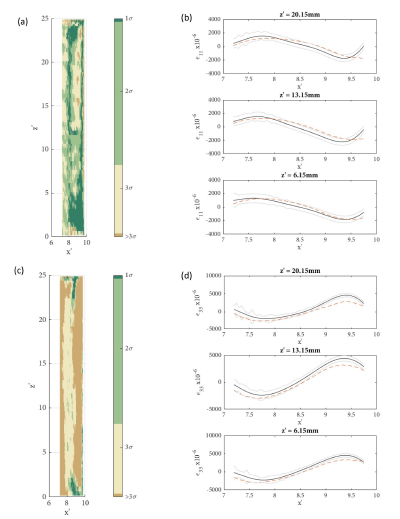
Click to Enlarge Image
In conclusion, the SIMULIA Additive Manufacturing Scenario app accurately analyzes thermal stresses in the AM process. Which enables build quality assessment before printing. Part of the 3DEXPERIENCE platform’s end-to-end AM flow, it has been experimentally verified and won first prize in the AFRL challenge, speeding up development and fostering innovation.