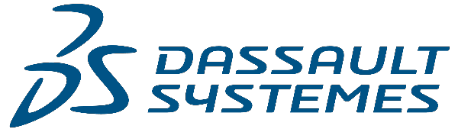
CATiA V5
Far beyond traditional 3D CAD software tools
CATIA is Dassault Systèmes’ pioneer brand. It is the world’s leading solution for product design and innovation.
Portfolios
Finding ways to reduce design-to-manufacturing cycles is a key priority for industrial companies. An accurate virtual definition of mechanical products is the answer but sometimes its construction is time consuming and design changes are complicated. Companies require a solution that is highly productive and flexible, without compromising design accuracy.
CATIA – Mechanical Product Creation provides the most complete and robust solution, tailored for any company that wants to make the difference by developing rapidly high-quality mechanical products with the highest productivity in design changes.
Included Modules
- CATIA – Part Design 2
- CATIA – Assembly Design 2
- CATIA – Generative Shape Design 1
- CATIA – Functional Molded Parts 1
Finding ways to reduce design-to-manufacturing cycles is a key priority for industrial companies. Companies need to rapidly design standard compliant sheet metal parts in 3D that are complex in addition to being ready-to-manufacture.
The CATIA Fabricated Product Creation option is dedicated to the rapid design of sheet metal parts. Designers benefit from already capitalized know-how and can take into account manufacturing constraints early in the design. In this way, they can create sheet metal parts that are fully compliant with company rules and standards for efficient manufacturing.
Included Modules
- Weld Design 1
- Sheet Metal Design 2
The modern manufacturing requires companies to reduce product development time and capitalize their know-how so that they can respond quickly to customer needs. In order to make it happen, they must expand their ability to innovate by automating redundant tasks and focusing on innovative projects.
CATIA – Jig and Tooling creation simply and quickly creates all the elements of tooling including structures (linear or curved), plates, using standard or user-defined sections, generic, and user tooling components. Benefiting from a rich variety of standard and user-defined components with embedded drilling and manufacturing information, the engineer is able to design faster than ever and to focus on added value tasks. Fully integrated in the CATIA environment, the designer is able, for instance, to seamlessly perform extensive stress analysis on his structure elements and beams, create drafting, or generate all information needed for NC programming.
Included Modules
- Tooling Design 1
- Structure Design 1
The process of designing and creating molded parts is often time-consuming and inflexible, which is incompatible with accelerating market trends for new design. Companies need to be equipped with state-of-the-art and highly productive technologies to maintain a competitive edge.
Molded product creation delivers ultra fast functional modeling for unmatched productivity and flexibility, to address the complete design-to-manufacturing preparation process of molded parts
Included Modules
- Functional Molded Parts 2
- Healing Assistant 1
- STL Rapid Prototyping 1
- Generative Shape Design 1
- Part Design 2
- Assembly Design 2
Now more than ever, mold manufacturers need to design faster and with the highest quality in order to differentiate themselves from the competition. Therefore, the tooling designer needs to maximize tooling automation creation to focus on the added-value tasks. In addition, designers should benefit from a single system that manages design changes throughout the design-to-manufacturing process.
The CATIA – Mold Tooling Creation option is dedicated to fast mold and stamping die design. Designers are able to reuse already capitalized tooling know-how, enabling rapid tooling creation fully compliant with company rules and standards. Seamless tooling design fosters concurrent engineering between the design office, tooling and manufacturing departments
Included Modules
- Core & Cavity Design 2
- Generative Shape Design 1
- Healing Assistant 1
- Part Design Feature Recognition 1
- Part Design 2
- Tooling Design 1
- Mold Tooling Design 2
- Assembly Design 2
In traditional systems, design modifications are very complicated, making collaboration between designers complex and delaying product development. Companies require an all-in-one solution to create and verify the quality of shapes.
CATIA – Mechanical Shape Design provides a unique and powerful spec-driven modeling approach for the creation of high-end mechanical shapes and the intuitive manipulation of free form surfaces. This standard solution for high quality surface modeling promotes efficient concurrent engineering between styling and shape design enabling to optimize the product design workflow.
Included Modules
- Generative Shape Design 2
- FreeStyle Shaper 1
- Developed Shapes 1
Companies need simple and ergonomic tools to rapidly morph shapes without altering their quality at any time during the design process.
CATIA – Mechanical Shape Optimization embeds unique breakthrough technologies enabling to perform quickly global morphing on complex shapes. It allows either to deform interactively shapes or to capture the realistic one based on real-world tests of the product in operation. This easy-to-use environment helps designers to achieve a real productivity gains to optimize the product or the tooling definition.
Included Modules
- Developed Shapes 1
- Generative Shape Design 2
- Generative Shape Optimizer 2
- Realistic Shape Optimizer 2
Composite materials bring forth many new possibilities and high performance products. Designers need dedicated tools in order to fully benefit from the potential that composites offer. A global environment requires trouble-free collaboration for designers who need to take composite manufacturing specificities into account early on.
The CATIA – Composites Design option provides engineers with a collaborative and completely CATIA-integrated environment to rapidly create innovative composite parts for the aerospace, automotive and shipbuilding industries. By enabling designers to work concurrently on the same design and to embed composites manufacturing constraints earlier in the conceptual stage, this option drastically shortens design time.
Included Modules
- Composites Engineering 2
- Generative Shape Design 2
Companies using 2D drawings to capture tolerance and annotation must maintain synchronicity between 2D drawings and 3D modifications in order to share consistent and up-to-date manufacturing information. This process is time consuming and error prone and does not permit further usage of 3D tolerance analysis or metrology.
CATIA – 3D Master provides 3D definition and management of standard-compliant tolerance specifications and annotations for parts and products. It transforms 3D as the master representation, directly re-usable for manufacturing planners and shared throughout the enterprise.
Included Modules
- 2D Layout for 3D Design 1
- 3D Func. Tolerancing & Annotation 2
The manufacturing constraints of molded and forged parts create a need for complex surfaces that are difficult and lengthy to design, and in most cases inflexible to modify. On the other hand, mass production parts require optimization to achieve the highest possible performance, while using the least amount of materials. Companies require highly productive technologies to focus more on innovation and less on modeling.
CATIA – Molded Product Design for Manufacturing accelerates detail design of cast, molded and forged parts with substantial productivity gains. Concurrently, designers create fully associative parting surfaces, cores and cavities of the most complex parts. The advanced process-driven functionalities avoid the need of complex and repetitive use of surface and wireframe operations and reduce learning activity.
Included Modules
- Cast & Forged Part Optimizer 2
- Functional Molded Parts 2
- Part Design 2
- Core & Cavity Design 2
- Generative Shape Design 1
Companies need to automate repetitive tasks in order to speed product development. Nowadays, it is crucial to reduce non valuable tasks time so to focus on job with high added value.
CATIA – Body & Skin Templates is an advanced option pack embedding unmatchable skilled features thereby helping streamline the Body in White design operations and strengthen the end-to-end process.
Included Modules
- Automotive Body in White Templates 2
- Generative Shape Design 2
Style
Work concurrently on style and engineering or perform simulation of a product’s appearance for quick style validation. Quickly capture physical prototype shapes and utilize integrated styling process to quickly launch new ideas into the marketplace.
Review and Optimization
Optimize product packaging, strength, and ergonomics while performing more complete product assessments earlier in the design process. Make quick and efficient decisions with advanced collaborative reviews—driving to ultimate product optimization.
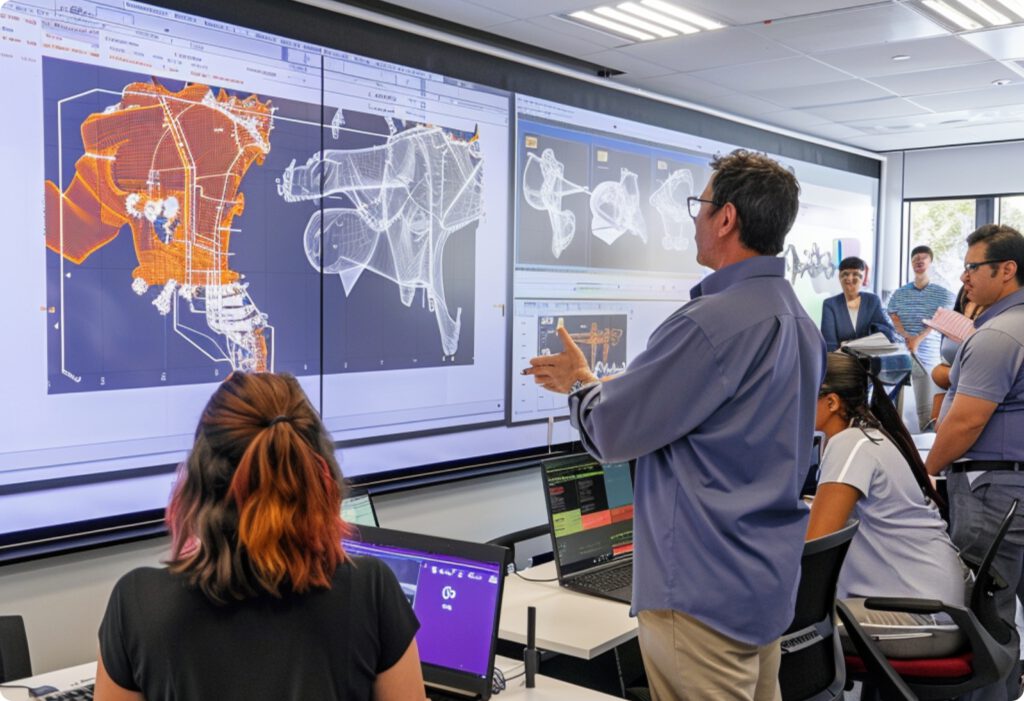
Generative Structural Analysis – GAE
Engineers need to optimize product design without sacrificing quality. They need to perform accurate analysis early in the design phase within an integrated and an easy to use environment.
CATIA – Generative Structural Analysis offers designers and engineers an easy-to-use analysis solution for simulating product mechanical behavior in the early phase of the design process.
Included Modules
- Generative Part Structural Analysis 2
- Gener. Assy Structural Analysis 2
Knowledge Advisor – KAE
In today’s competitive market, efficient decision making and accurate designs are the crucial elements of success. Because competition drives innovation, the product needs to generate the highest quality in the shortest amount of time.
CATIA – Knowledge Advisor allows designers and design engineers to capture their know-how and re-use it as best practices. Users can embed knowledge into their design through formulas, rules, reactions and checks. By accelerating the exploration of design alternatives with regard to rulesn, users makes better decisions and reach optimal, error-free designs quickly.
Included Modules
- Knowledge Advisor 2
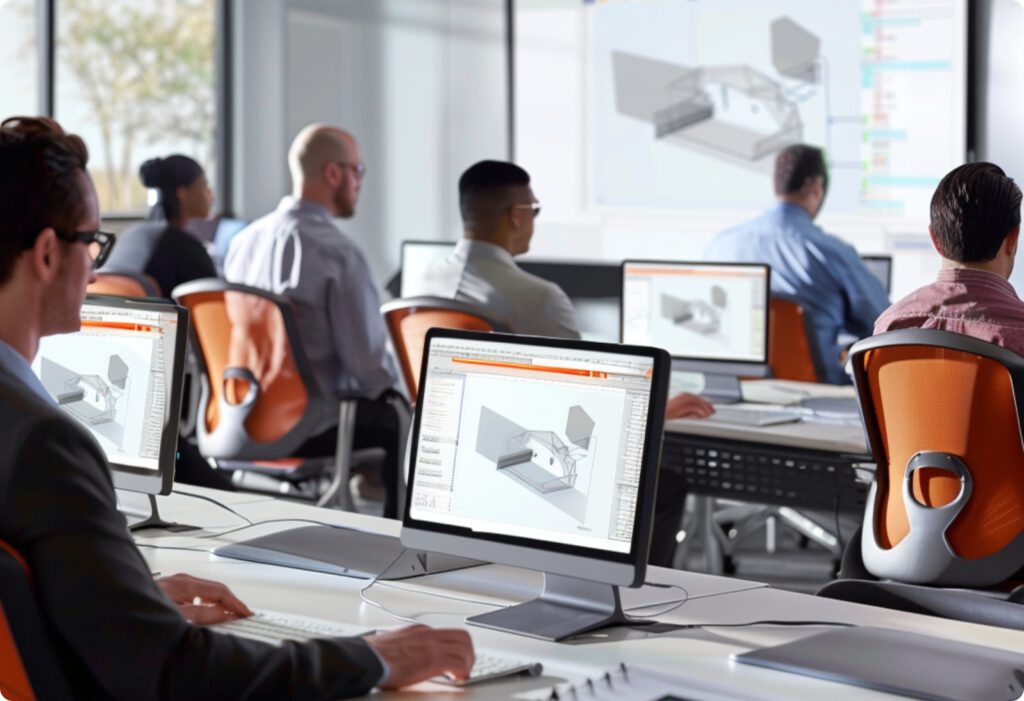
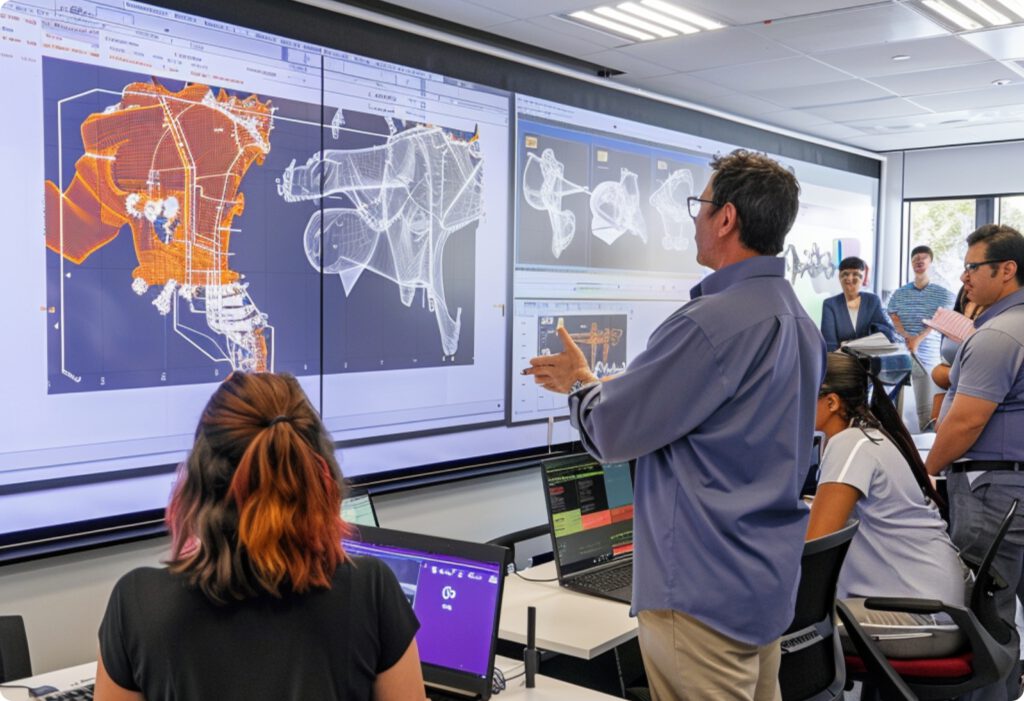
Technological Specifications Review – TRE
Global demand and breakthrough technologies are increasing the complexity of product designs and the supply chains needed to build them. These distributed organizations need a way for stakeholders to view, understand and evaluate a virtual product definition.
CATIA – Technological Specification Review enables to place 3D product definition at the heart of people interactions and communications. It gives access to critical product information including functionnal annotations and tolerancing, fasteners types and positions and finitie element analysis results. It also provides companies with a way to filter sensitive information before sharing 3D designs with partners.
Included Modules
- DMU Engineering Analysis Review 2
- Product Data Filtering 1
- DMU Fastening Review 2
- DMU Dimensioning & Tolerancing Review 1
FEM and Structural Analysis – FAX
Today, companies need to control their development costs, while especially focusing on the costs of physical prototypes. They also need a solution that combines design and analysis in order to validate and optimize product development.
CATIA – FEM & Structural Analysis delivers a complete finite element modeling and analysis solution covering a wide range of structural analysis processes. Fully integrated within the CATIA design environment, it promotes seamless product design quality improvement.
Included Modules
- Generative Part Structural Analysis 2
- Gener. Assy Structural Analysis 2
- FEM Surface 2
- FEM Solid 2
- Gener. Dynamic Response Analysis 2
- Elfini Structural Analysis 2
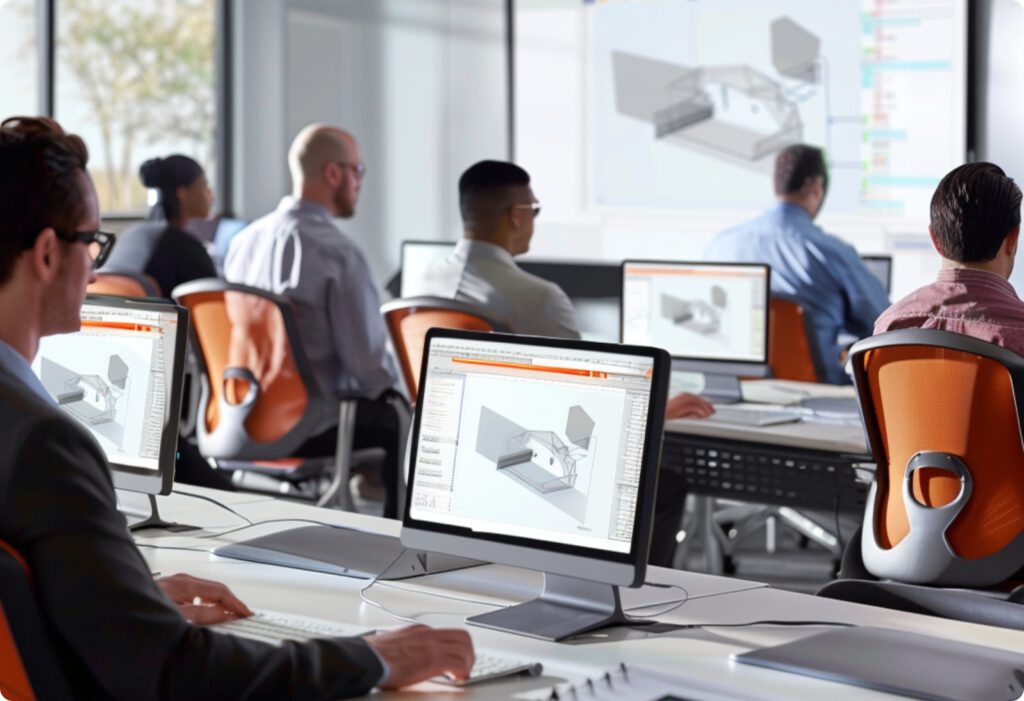
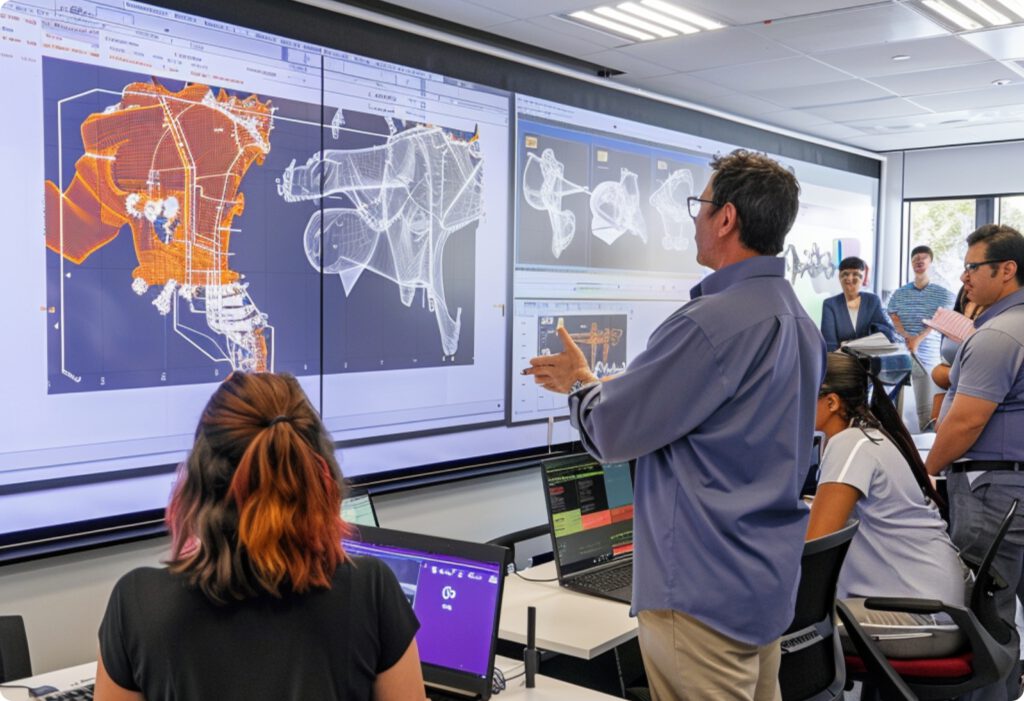
Animated Product Review – PRX
Manufacturers must overcome unique technical and strategic challenges to keep pace in today’s virtual global marketplace. As global demand and breakthrough technologies increase the complexity of product designs, engineers need more advanced desktop tools to quickly validate and release designs into production.
CATIA – Animated Product Review provides a comprehensive set of tools to simulate complex product behavior in one unified environment. This enables more decisions in the virtual stage of development — before investing in expensive prototypes, production resources, and product launch activities.
Included Modules
- DMU Fitting Simulator 2
- DMU Space Analysis 2
- DMU Kinematics Simulator 2
Knowledge Expert & Engineering Optimization – KOX
Product designs that continue to use physical prototypes are prone to errors, delays, and increased expenditures. Companies need built-in knowledge that ensures a product’s conformity to various standards, thus saving time and expenses, and reducing errors.
CATIA – Knowledge Expert provides a powerful interactive environment to create and manage validation rules in order to ensure that product designs conform to industry, customer or company standards.
Engineering Optimization provides an interactive environment for modeling and solving complex engineering problems.
Included Modules
- Product Engineering Optimizer 2
- Knowledge Expert 2
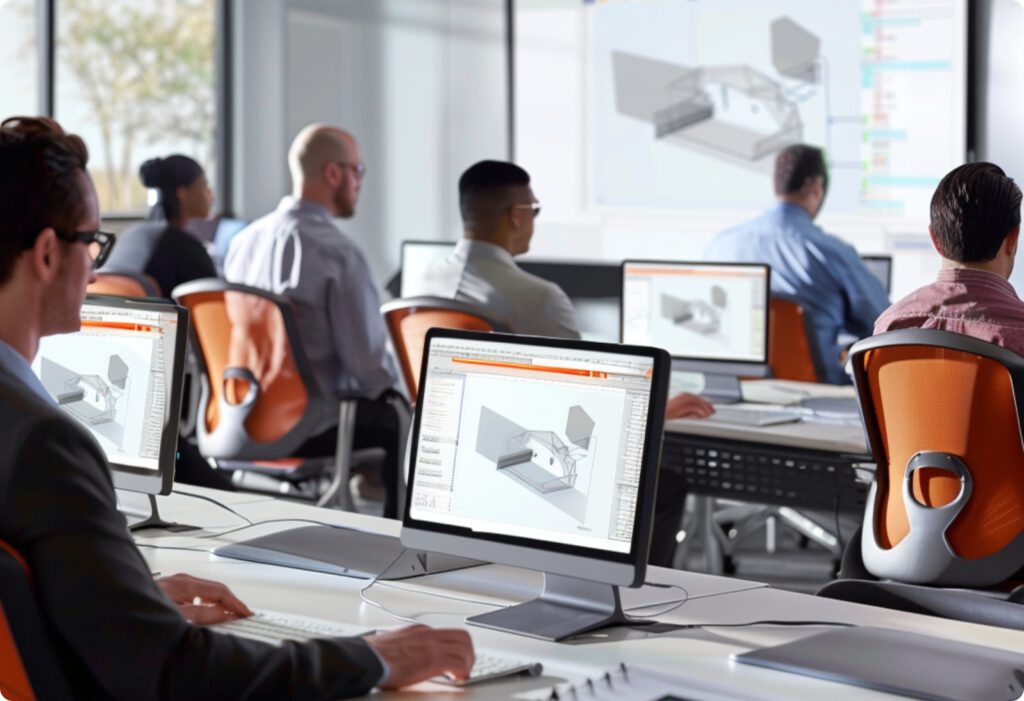
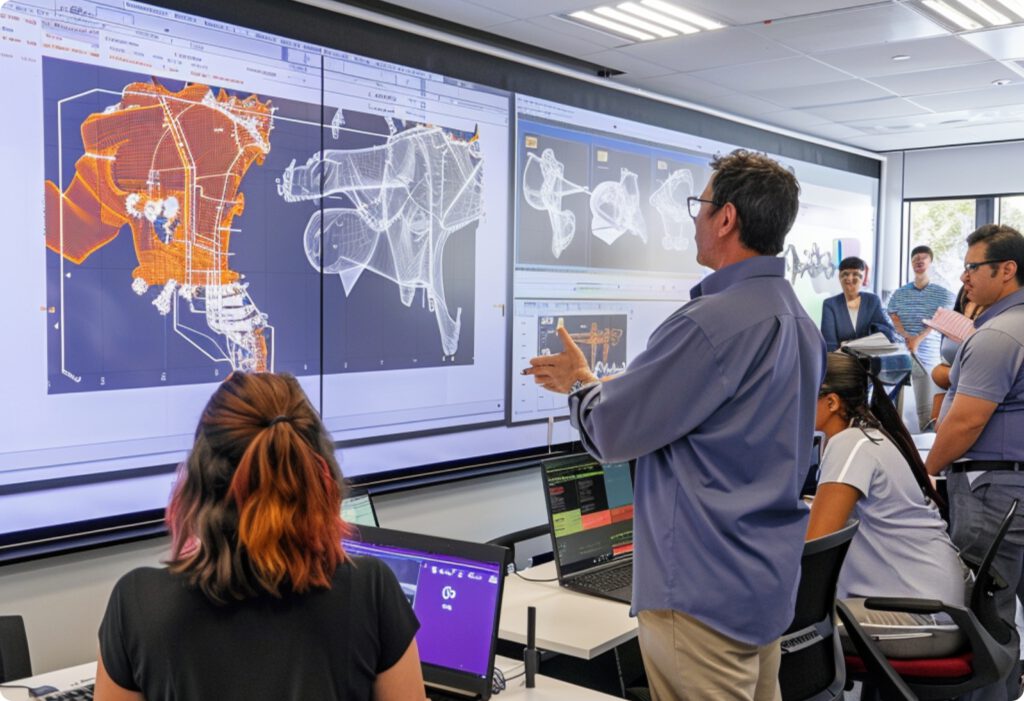
Human Builder & Simulation – HSX
The human being is one of the most non-standard and unpredictable components of any system. Human capability is a major (limiting) parameter of design, then in many application areas there is a strong requirement to model the physical elements of the human alongside product designs.
CATIA – Human Builder and Simulation enables to directly create, manipulate and simulate accurate digital manikin’s interactions in context with the virtual product. It is the only solution enabling to assess and optimize human posture, vision and comfort directly in the product design environment, leading to fast decision making and design changes. Accurate human modeling, postures and comfort information capitalization makes company’s know how on ergonomics available to all designers.
Included Modules
- Human Builder 2
- Human Measurements Editor 2
- Human Posture Analysis 2
- Human Activity Analysis 2
- DMU Space Analysis 2
Equipment and Systems Engineering
Easily define equipment and visualize a complete virtual product, reflecting both mechanical components and other systems such as fluid and electrical. Experience realistic simulation in an integrated environment to reduce design time and increase the quality of large scale systems.
Manufacturing standards and norms play an essential role early in the product conception phase, and must be considered throughout product design. The lack of built-in catalogs and specifications increases design time and costs.
CATIA – Piping Schematic to Design product enables the user to design and manage logical lines of piping systems using standards and specifications according to industry usage. It enables creation of component catalogs with multi-representation, attributes and design rules. The system engineer creates intelligent schematics piping diagrams.
Fully integrated, the piping designer builds the 3D design directly from 2D diagrams (2D/3D driven). Theses intelligent diagrams and 3D design capability enable users to create and validate their designs with respect to company know-how.
This product covers project engineering from basic design up to detailed design.
Piping versus Tubing: Piping standard components such as valves and flanges are welded or bolted with straight pipes.
Included Modules
- Piping Design 2
- Piping and Instrumentation Diagram 2
- Systems Diagrams 2
The lack of an associative environment between 2D schematics and 3D HVAC design leads to unnecessary errors and design delays. Companies need an integrated solution to design logical lines of HVAC systems in order to validate the design early in the design process.
CATIA – HVAC Schematic to Design product (1) enables the user to design and manage logical lines of HVAC systems using standards and specifications according to industry usage. It enables the creation of component catalogs with multi representation, attributes and design rules. The system engineer creates intelligent schematics and HVAC Diagrams.
Fully integrated, the designer builds the 3D design directly from 2D diagrams (2D/3D driven). These intelligent diagrams and 3D design capability enable users to create and validate their designs with respect to company know-how.
This product covers project engineering from basic design up to detailed design.
(1) HVAC: Heat, Ventilation and Air-Conditioning
Included Modules
- HVAC Design 2
- HVAC Diagrams 2
- Systems Diagrams 2
Early in the product conception phase, companies need to take into account manufacturing standards and norms. The lack of built-in catalogs and specifications increases design time and costs.
CATIA – Tubing Schematic to Design product enables the designer to design and manage logical lines of tubing systems using standards and specifications according to industry usage. It enables the creation of component catalogs with multi-representation, attributes and design rules. The system engineer creates intelligent schematics tubing diagrams.
Fully integrated, the tubing designer builds the 3D design directly from 2D diagrams (2D/3D driven). These intelligent diagrams and 3D design capability enable users to create and validate their designs with respect to company know-how.
This product covers project engineering from basic design up to detailed design.
Tubing versus Piping: tubing lines are manufactured using a bending process. The diameter is usually smaller than piping. Tubing lines may include flexible tubes.
Included Modules
- Tubing Design 2
- Systems Diagrams 2
- Tubing Diagrams 2
It is increasingly necessary to embed electrical components that require optimized cable connections in industries such as industrial equipment, high-tech, and consumer goods. Electrical designers need to integrate their modules and cables early in the process to avoid costly physical prototypes.
CATIA – Electrical 3D Design & Documentation provides a dedicated electro-mechanical end-to-end solution for designing and documenting electrical modules in all industries that design electric, electronic and electro-mechanic components. It reduces time and cost for creating electrical modules directly in the Digital Mock-Up, avoids interferences and create up-to-date manufacturing documentation.
It addresses also suppliers who design independent electrical modules that interface with a global electrical digital mockup, especially when OEM’s are equipped with CATIA V5. (End-to-end auto or aerospace large wire harness design is addressed with CATIA – Electrical Wire Harness Design and CATIA – Electrical Wire Harness Flattening)
Included Modules
- Electrical 3D Design & Documentation 1
Today’s consumers require compact electronic devices with greater functionalities. To create high-quality products faster, companies need integration of realistic PCBs inside a virtual product and simplified collaboration between mechanical and electronics specialists.
CATIA – Flexible PCB Design enables modeling of a flexible circuit board within a virtual mock-up and facilitates collaboration with electronic CAD systems.
Included Modules
- Circuit Board Design 1
- Sheet Metal Design 2
Once a product is ready to manufacture, its design must be precise or it risks costly errors and delays. Collaboration is the essential key to successful documentation and design between harness designers and manufacturing.
CATIA – Electrical Wire Harness Flattening provides automatic and complete flattening of 3D Electrical Harnesses for manufacturing documentation in a concurrent engineering environment.
Included Modules
- Electrical Harness Flattening 2
- Electrical Library 2
- Electrical Wire Routing 2
The design of large-scale electrical systems requires a process-specific solution in order to save time and ensure design quality. The use of physical prototypes is expensive, demonstrates design errors late in the process, and is inflexible to modifications.
CATIA – Electrical Wire Harness Design delivers a process oriented solution for designing physical wire harnesses driven by logical specification and integrated with harness manufacturing. By delivering a realistic simulation for 3D wire harness packaging in an integrated environment, this powerful solution reduces design time and increases the overall quality of large scale electrical systems.
Included Modules
- Electrical Wire Routing 2
- Electrical Library 2
- Electrical Harness Installation 2